Innovative Processing of Apparel
Flat and Low-friction Seams via Laser Welding
Machine sewing, hot-air welding, and ultrasound are well-known procedures applied in the finishing of clothing.
Laser welding is a completely new technology used in the clothing industry. The Swiss company Leister Technologies AG is developing this market to industrial maturity. Promising garment prototypes are already being produced. We spoke to project manager Frederike Lehmeier about this new process. “Compared to ultrasonic welding, laser-welded seams have an undamaged fabric surface; melting points are not visible on the surface. Adhesive material is not required either,” she explained the advantages.
Laser welding is therefore particularly interesting for functional clothing: the seams can be extremely flat, elastic, and therefore skin-friendly. A so-called seamless effect can be achieved because the outside of the materials to be welded is not damaged. This technology is based on laser transmission welding, in which fiber-guided diode lasers are used in the near IR (NIR) range.
Laser transmission welding requires working with a laser-transparent and a laser-absorbing material. These two materials are joined exclusively between both material layers. Another possibility is the use of exclusively transparent materials; in this process, absorbers are partially applied to the positions to be welded.
The basic rules of laser welding:
Beyond Borders

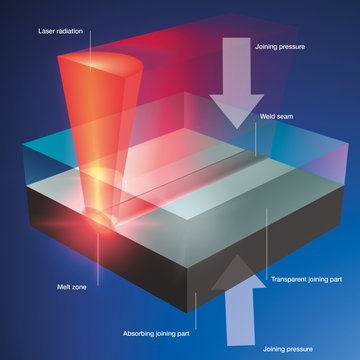
- Transparency and absorption are required
A laser transmission weld requires a transparent and an absorbent textile when lasers with a wavelength of 940 nm are used. - Welding same with same
In laser welding, thermoplastic materials are joined together. During the welding process, laser radiation is absorbed by plastic and converted into heat. Thermoplastics are plasticized in the joining zone and joined under pressure.
In order to achieve a connection with high strength, similarly-typed thermoplastics should primarily be used. Practically speaking, this means, for example, that polyester can only be welded with polyester and polypropylene only with polypropylene.
Working with the same materials has a positive ecological impact on a subsequent recycling process and is becoming important for increasingly sustainable production in the textile and clothing industry.
Materialization
Beyond Borders
Materials tested to date in the textile and clothing industry include single-layer elastic and non-elastic knitted and woven fabrics, spacer fabrics, nonwoven materials, membranes between 10 µm and 25 µm, and multi-layer textiles (laminates). The chemical basis is largely polyester articles and, for knitted fabrics, polyamides and polypropylene articles.
In addition to polyester products, polyurethane-based materials can also be welded. The low foreign fiber content of a material type (e.g., elastane) does not significantly influence the laser welding process and the seam quality as long as they have laser-transparent properties.
Many of the textile materials available on a standard basis have laser-transparent properties. It is more difficult to use materials with sufficiently high absorption; they usually have a dark shade. Working with absorbent and transparent materials is often accompanied by a two-tone appearance.
If this is not desired, purely transparent materials can also be processed together “using a trick:” Either mostly liquid, NIR-absorbing pigments (absorbers) are introduced or additional absorbent materials are used.
Application Fields and Seam Shapes
Beyond Borders

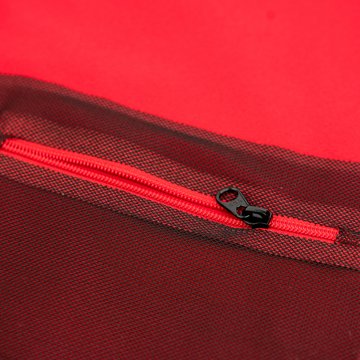
Low-friction, flat, and flexible laser welds are ideal for garments that come into contact with the skin. This increases the wearing comfort of underwear, swimwear, sportswear, and fitness clothing – an enormous benefit for sweaty athletes who wish to enjoy the highest wearing comfort! This has been successfully tested in practice.
Two main seam shapes are used for textiles.
Seam shapes for two-dimensional connections are used, for example, for attaching pockets but also for decorations, reinforcements, or fixing insulating materials to outer fabrics. This technology can be particularly interesting for the continuously growing wearables market if sensors and other technical components are incorporated directly into the clothing.
Three-dimensional, shaping seams are used, for example, for overlapping seams, hemming seams or the welding of strip materials.
Outlook
Beyond Borders

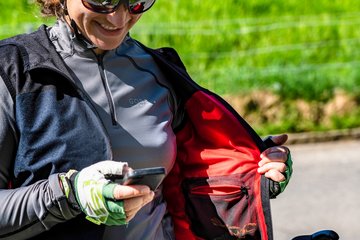
Laser welding yields a new joining technology for clothing, textile products in medical technology, and technical textiles. Manufacturers and brands in the textile and clothing industry have a high need for innovation and differentiation in a highly competitive market. This development takes into account innovative laser technology.
Leister pioneered the development of textile-specific laser machines. We are working on making the sophisticated processing of textiles industrially accessible by means of suitable machines.

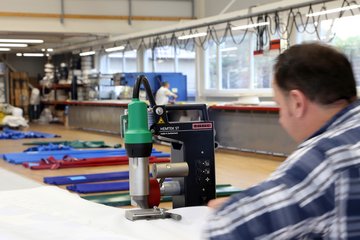
Leister Technologies AG is developing two machine concepts for processing textiles.
A two-dimensional cutting and welding system for the clothing industry will be available as early as 2019. This laser system is based on a vacuum table and can draw in up to three layers of material. Welding and cutting is carried out completely automatically, and different tool heads are applied for each process step. Globo Optic is used for laser welding. The cutting process is performed using a knife tool, which can be selected depending on the material being processed. An inkjet printing head can be integrated on an optional basis to print absorbers on transparent textiles.
In 2020, a continuously manually-operated laser sewing machine will be available as a standard product for shaping seams. In this development, laser technology is integrated into the mechanical engineering process that is well known in textile and clothing technology. This operation is carried out for the user with the help of a similarly familiar methodology. Machine designs and dimensions, as well as the classification as laser class 1, allow positioning in a conventional production line.
LASER COMPONENTS Nordic - Your competent partner for optical and optoelectronic components in Sweden, Norway, Finland, Denmark, and Iceland.
Welcome to LASER COMPONENTS Nordic AB, your expert for photonics components. Each product in our wide range of detectors, laser diodes, laser modules, optics, fiber optics, and more is worth every Crown (SEK). Our customized solutions cover all conceivable areas of application: from sensor technology to medical technology. You can reach us here:
Box 14001 / Skårs led 3
SE-400 20 Göteborg
Sweden
Phone: +46 (0)31 703 7173
Email: info(at)